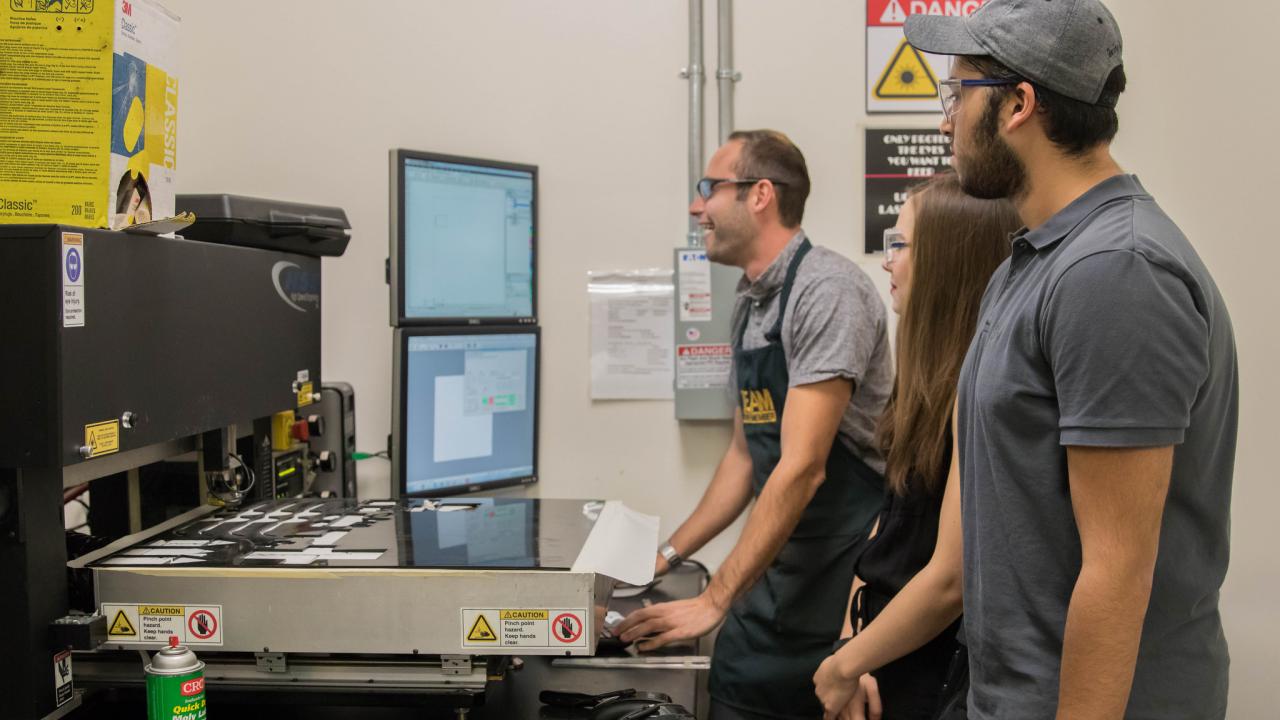
TEAM Electrical/Mechanical Lab Is Here to Help All Makers
Cutting-edge technology and professional assistance make clients’ designs happen
Prosthetics, medical models and so much more: There’s always something happening in the UC Davis Biomedical Engineering TEAM Lab.
“Translating Engineering Advances to Medicine” is the lab’s mission. Located on the first floor of the UC Davis Genome and Biomedical Sciences Facility, it’s a unique place that empowers researchers to take a health- or life-improving idea and make it a reality with the help of experienced staff and amazing design and manufacturing technology.
“If you have a concept, idea or objective, we’re here to help,” said TEAM Lab Manager Steven Lucero.
Location, Location, Location
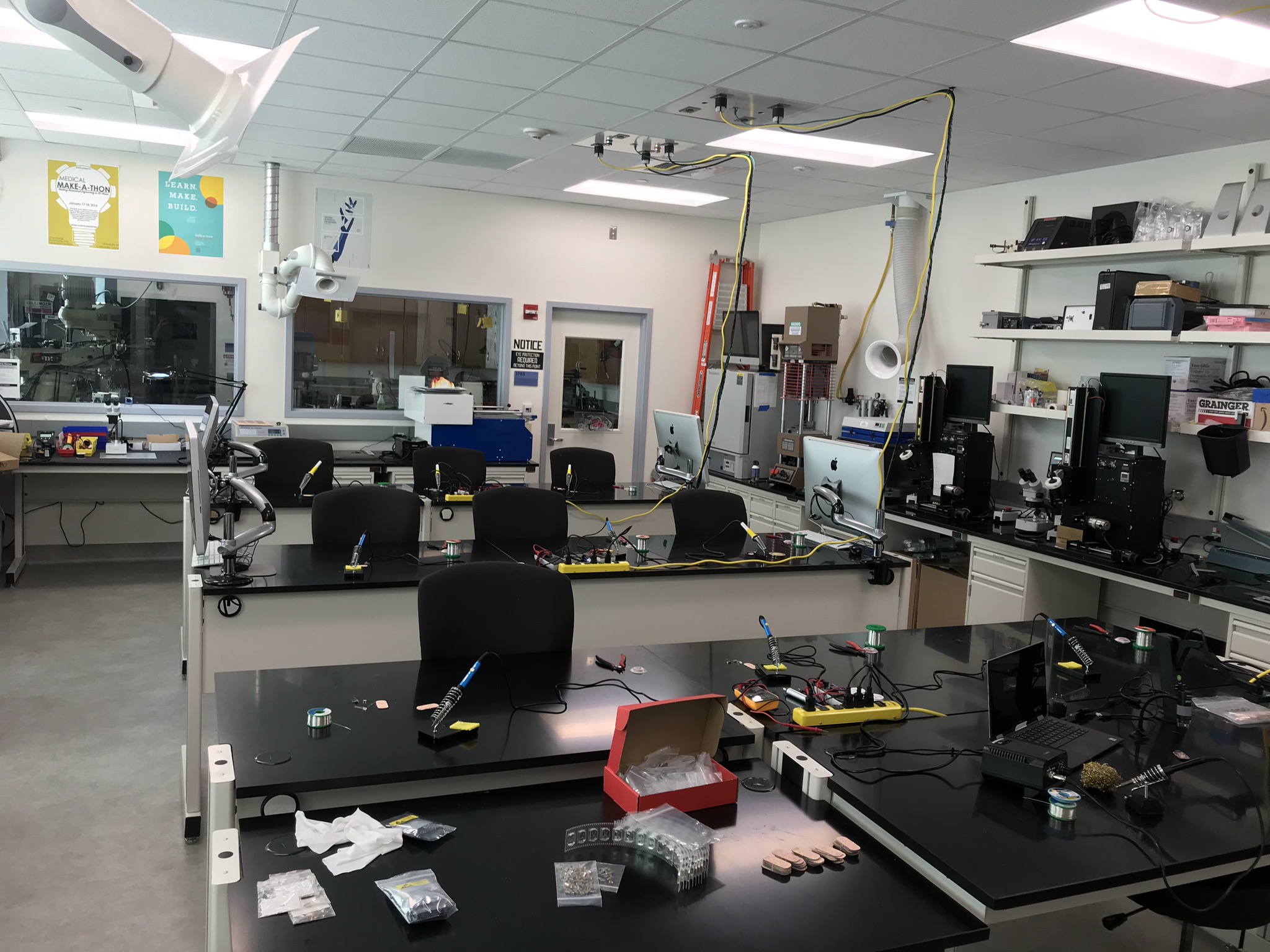
The UC Davis Biomedical Engineering Department’s first, small machine shop was on the second floor of the building, but there were complications: space on that floor was at a premium, the equipment was neglected and there was no on-site assistance for those who would wished to use what tools there were.
Enter Lucero, a mechanical-engineering UC Davis grad who signed on for a temp job simply to move the equipment to a little-used first-floor classroom. Instead of just moving the equipment, Lucero organized and refurbished each item and created a usable space in the new location. A six-month gig turned into six more months, then a year and beyond: More and more people started coming by, and armed with his mechanical-engineering knowledge, Lucero was happy to help everyone fabricate their designs. BME department leaders took notice and started asking him for his opinions on what other equipment the lab could use, and his suggestions were acted upon.
“We got our very first 3D printer for a few hundred dollars,” he recalled. ”But then we got a new and better one, and then a newer and better one, and we just kept adding and improving.”
Equipment additions to the first-floor space created a need for more room, so department leaders found a second spot down the hall. While helpful, the annex made for much back-and-forth in Lucero’s efforts. So in 2016, the lab finally took its current form, with 3D printing, machining and laser-cutting equipment all in the same roomy, user-friendly first-floor area with Lucero and student-assistants there full-time to help.
“I like being someone people can depend on to realize their design and manufacturing goals,” said Lucero. “My job in one word is ‘variety!’”
Technology transforms ideas into reality
The maker-space now boasts a fantastic array of the latest equipment, including:
- 3D Printing — The facility has a variety of 3D printers that use materials such as resin, plastic and polymer to suit products different strength needs, including a brand-new 3D Carbon printer that uses pixels to measure where to place material.
- 3D Scanning – The lab’s 3D scanner scans three-dimensional objects into a computer-aided design (CAD) format that then can be uploaded to the printers or other equipment for manufacture.
- Circuit-Board Manufacturing – Many creations need circuitry to work, so the lab has its own printed-circuit-board mill.
- Laser Cutting and Engraving – The lab’s laser cutter can cut and engrave wide varieties and thicknesses of materials.
- CNC Milling and Metal-Working Lathe – A computer-aided industrial mill and lathe are on hand for machining steel, aluminum, wood, plastics and much more to clients’ specifications.
“While it’s very unusual for an actual college to have equipment of this caliber, I haven’t heard of another department anywhere that has this type of lab and equipment of its own,” said Lucero.
Here to help everyone
But that doesn’t mean the Biomedical Engineering Department’s the only one that can use the lab: While department members can do hands-on work with the equipment, everyone’s welcome, with non-department clients receiving the professional services of Lucero and highly trained student-employees. The facility’s now so popular that three student-employees are needed to help Lucero take care of all clients, whose projects – from simple laser engravings to true-to-life 3D-printed hearts — now number about 1,200 each year.
“I couldn’t do it without the students!” he said. “They work on their own projects, senior students serve as an advisory committee to help clients with their designs and some students even work here as employees. Students truly are part of our ‘TEAM.’”
Valerie Quiroz, a student-employee who is a mechanical-engineering major and a BME minor, came to be part of the TEAM lab after visiting with a tour.
“We have the opportunity to be on top of the most advanced research,” she said. “We’re making things that have never been made before.”
“I enjoy the production side of things and working with my hands,” added TEAM student-employee Ben Lugten, a rising BME senior who also was inspired to sign on during a student tour. “I feel totally at home here.”
And what’s more, the electrical/mechanical TEAM Lab can work in tandem with the newer molecular/biological TEAM Lab for hybrid projects, such as devices with integrated molecular and electro-mechanical materials.
“We’re here to assist people through the whole process,” said Lucero. “Guidance and development all the way to the finished product – whatever that product may be — the TEAM Lab can make it happen.”
For more information
For more information on the TEAM electrical/mechanical lab, including services, equipment, donations, pricing and appointments, please visit team.ucdavis.edu.